ماكينة تصنيع القش PLA
Are you looking for a machine to manufacture biodegradable straws? KEZHI offers you quality assurance, reliability and excellent value.
يمكن أن توفر لك Machinery Kezhi خط إنتاج ممتاز لجعل مشروعك نجاحًا.
المنتجات كيجي يقدم لك
Kezhi هي شركة تصنيع رائدة متخصصة في تطوير وإنتاج آلة صنع القش المختلفة ، آلة تعبئة القش ، آلة الانحناء القش. لقد وضعنا التزامنا بالجودة كمزود لحلول إنتاج القش من الدرجة الأولى على نطاق عالمي

ماكينة تصنيع القش PLA
- Main screw diameter 65mm/50mm
- Delta Inverter,WN motor,
- Maximum output 100kg/hour
- Suitable for PP/PLA straw making
- Auto material loader/dryer

ماكينة تصنيع القش PLA
- Servo motor, direct driven, Delta Inverter,
- Main screw diameter 65mm/50mm
- Maximum output 100kg/hour
- Suitable for PP/PLA straw making
- Auto material loader/dryer
General Applications For The Production Line
The line can be used to make not only beverage straws, but also coffee stirrers, lollipop sticks, nozzle tubes, pen refills and other small profiles by changing the molds, providing more options for your production.
مقدمة من آلة
Our PLA Straw Making Machine represents a cutting-edge solution for producing biodegradable drinking straws from Polylactic Acid (PLA), a sustainable and eco-friendly material derived from renewable resources like corn starch, sugarcane, or cassava. Designed to replace traditional plastic straws, these machines offer a practical step towards reducing environmental pollution.
Main Components:
- Extruder: Efficiently melts and extrudes the PLA material into straw form.
- Cooling Water Sink: Rapidly solidifies the extruded straws, ensuring they maintain their shape.
- Hauling Machine: Delivers consistent pulling force to draw the extruded straws through the production line.
- Cutting Machine: Precisely cuts the straws to uniform lengths according to specifications.
- L Shaped Straw Collecting Machine: collect the straw more easily, operator can get the straw to next station faster.
Versatility and Additional Equipment:
- Material Flexibility: While optimized for PLA, the machine can also process other biodegradable materials such as PP (polypropylene) and PHA (polyhydroxyalkanoates), adding versatility to your production capabilities.
- Complete Production Line: Often integrated into a comprehensive production line that might include additional units like straw bending machines, packing machines, and carton boxing machines, offering a complete solution from production to packaging.

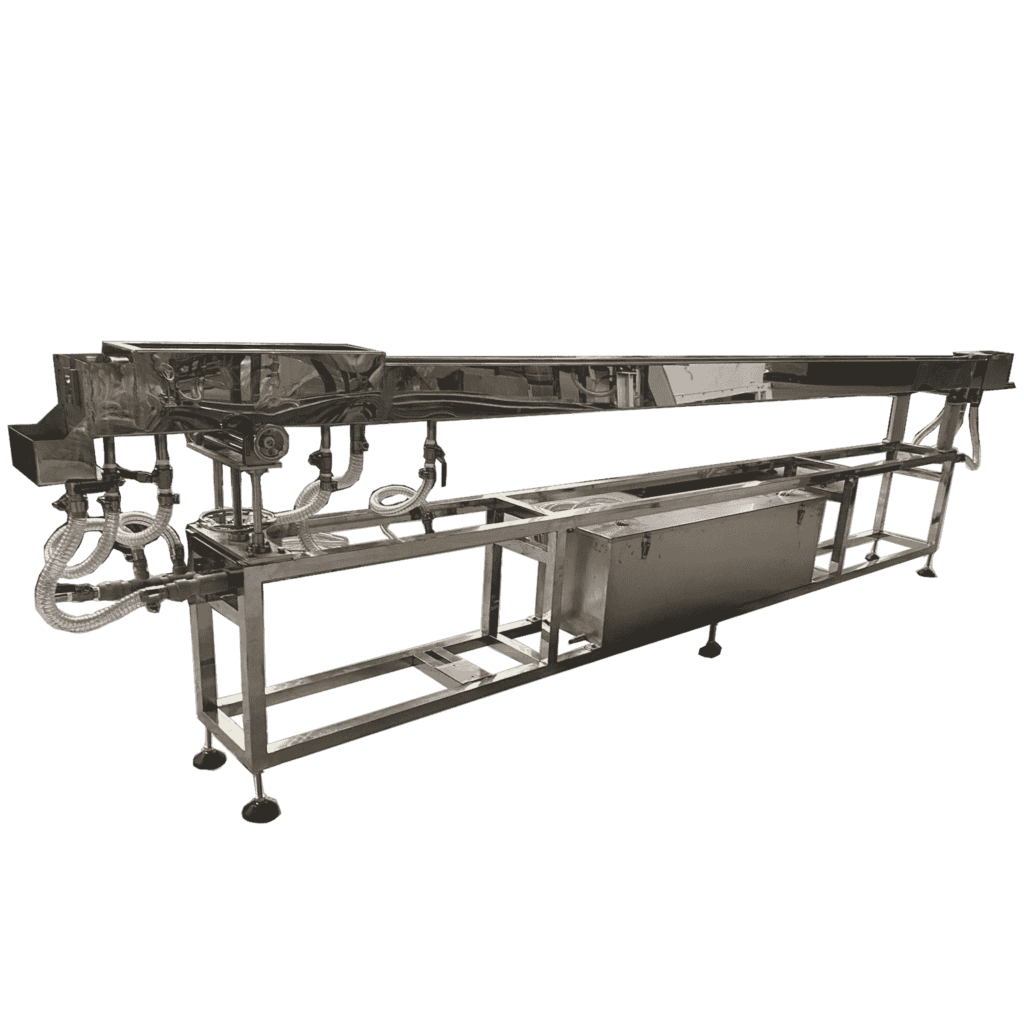


Features of الطارد
The most important part of the production line, where the tubing is extruded
Temperature control
Cast aluminum heating, which is fast and gentle heating, dedicated to the production of high-end pipes, and does not cause secondary damage to the extruded material.
Main Screw
Special designed 65mm/50mm screw to meet the characteristic of bioplastic material.
L/D: 33:1
meets the production of PLA and PP materials.
Cooling
six sets of fan cooling
Driving Motor
Using 11KW/ 30Kw three-phase asynchronous motor, output torque is bigger, production is more stable, the product is mature and easy to maintain.
Servo motor optional
Gear Reducer
Special hardened gear reducer for plastic extruder, Guomao brand, reliable quality,
Ratio 12.5
Inverter
Delta inverter, famous brand, stable and reliable performance, the most recognized inverter in the straw industry
Cooling water sink features
In the second part of the line, the extruded pipe will be cooled and better shaped here.
- Material
Stainless Steel, No rust, longer lifetime
- Water tank
Equipped with a water tank, allows you to connect with the water chiller directly
- Adjustability
The direction of the cooling water sink can be adjusted,
- Length
Two options, 3.5 meters, and 4.5 meters
- Temperature required
The water temperature inside the water sink shall be 25-30 degrees (for PP material)


Traction & Cutting Machine features
In the third part of the line, the extruded pipe will be pulled and cut into small pieces here.
Required المعدات المساعدة
These two machines are necessary for the production line running.

المبرد الصناعي
A 5HP industrial chiller is required for the production line, you can choose an air-cooled chiller or water-cooled chiller on your needs. Flow requirement: over 3 cubic meters per hour

Air Compressor
A 7.5KW(10hp) air compressor is required for a single production line, you can choose pistol air compressor or screw air compressor on your needs.
كيف يعمل
من هذا الفيديو ستكتشف كيف يعمل ،

لماذا PLA Straw
Know more about PLA straw
What is PLA Straw?
PLA biodegradable straws are made from polylactic acid (PLA), a type of bioplastic derived from renewable resources like corn starch or sugarcane. Unlike traditional plastic straws made from petroleum, PLA straws are designed to be compostable under industrial composting conditions.

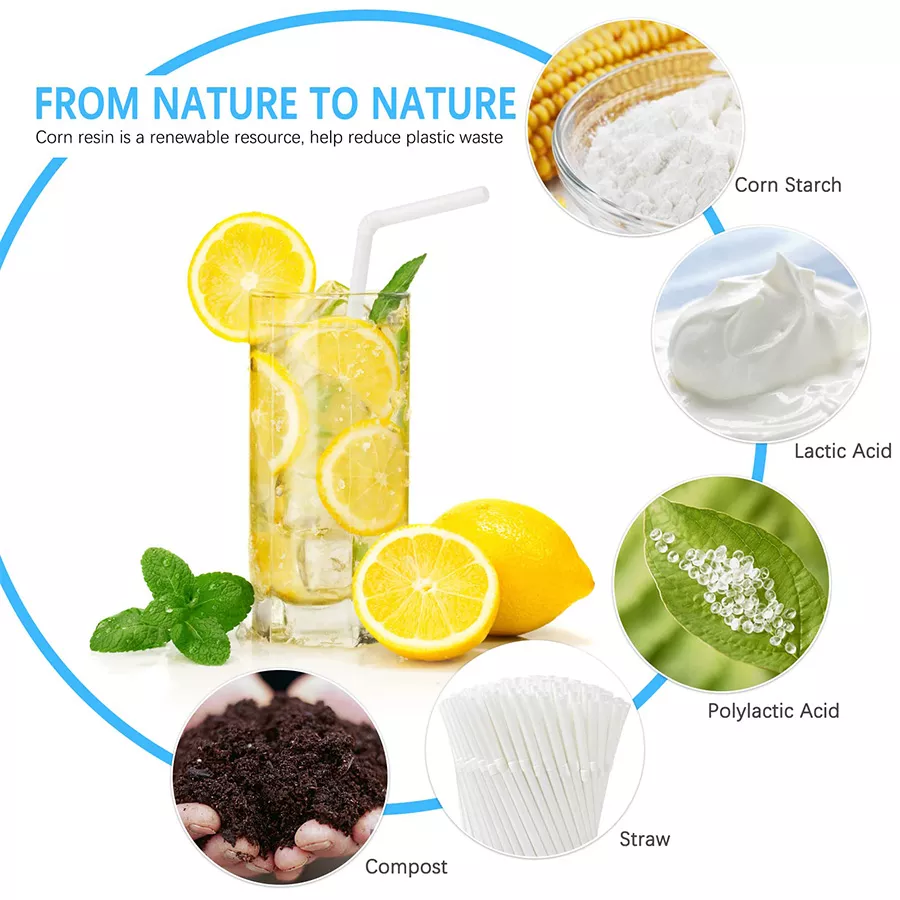
Polylactic Acid (PLA) is a biodegradable and biocompatible thermoplastic polymer derived from renewable resources such as corn starch or sugarcane. It is produced through fermentation and polymerization processes, forming an aliphatic polyester with the chemical formula C3H4O2. PLA consists of three main sub-families—PDLLA, PLLA, and PDLA—each featuring unique molecular structures. This polymer is known for its high strength yet brittle nature, with a density of 1.27 g/cm³, a tensile strength of 59 MPa, and a melting point of 165°C. Despite its biodegradability, PLA requires specific conditions like 60°C temperature and 90% humidity to decompose fully. Common applications of PLA include 3D printing filaments, medical devices and implants, food packaging, and textiles. Its eco-friendly properties, lower energy requirements for production compared to traditional plastics, and general food safety make PLA a popular choice across various industries, particularly in additive manufacturing and medical fields.
Advantages of PLA straw
1. Biodegradability: Under the right industrial composting conditions, PLA straws are biodegradable. They decompose into water and carbon dioxide through the action of environmental microbes, typically within 90 days in suitable composting environments.
2. Plant-based Material: Made from renewable resources like corn starch, PLA straws serve as a more sustainable choice than straws made from petroleum-based plastics.
3. Food Safety: PLA straws meet food-grade standards and are safe for use with both hot and cold beverages.
4. Variety: Available in various sizes, shapes, and colors, PLA straws can meet diverse needs and preferences.
5. Cost Efficiency: The cost of PLA straws is about 2 cents each, which is comparable to traditional plastic straws and more economical than paper straws, which cost about 4 cents each.
6. Advanced Formulations: Enhanced versions of PLA, such as stereo-complexed PLA (SC-PLA), offer better heat resistance, mechanical strength, and moisture stability than standard PLA straws.
7. Recyclability: Certain advanced formulations like SC-PLA might be recyclable, providing an advantage over typical single-use biodegradable straws.
8. Environmental Benefits: PLA straws are deemed safer for wildlife because they soften in liquids and break down quicker than plastic straws.
The Basic Knowledge عن Plastic Extrusion Machine
A brief introduction to plastic extruders to help you get a basic understanding of the machine
Table of Contents
What is plastic extrusion machine?
Plastic extrusion is a high-volume manufacturing technique in which raw plastic, typically in pellet form, is melted and extruded into a continuous profile. The process initiates as the resin is loaded into the extruder’s hopper and moves down into the barrel, where it is progressively heated until it melts. Following this, a screw mechanism drives the molten plastic through a die, which molds it into the required shape. As it cools and solidifies, it assumes the final form of various products, ranging from pipes and plastic sheeting for weather-stripping to wire insulation. This method is highly valued across various industries for its efficiency, versatility, and consistent ability to produce large volumes.
Working principle of plastic extruder
The Role of Extruders in Plastic Extrusion
Extruders serve as the core component in the plastic extrusion process, consisting primarily of a heated barrel outfitted with a rotating screw. The process begins with the introduction of raw plastic materials, typically in pellet form, into the extruder via a hopper. As the screw rotates, it drives the pellets forward into the barrel, where they encounter significant heat and pressure, causing them to melt into a viscous fluid. This fluid plastic is then extruded through a die—a tool engineered to mold the plastic into the specified profile as it emerges from the machine. The plastic product is subsequently cooled and solidified, retaining its shape as it is segmented into predetermined lengths. This method is crucial for producing continuous lengths of plastic in diverse shapes, thereby playing a pivotal role in various industrial applications.
Components of a Plastic Extrusion Machine
A standard Plastic Extrusion Machine is composed of several key components, each playing a crucial role in the extrusion process:
1. Hopper: The initial entry point for the raw plastic material, generally in pellet form. The hopper channels the material into the extruder’s barrel.
2. Barrel: This component encases the extruder screw and is fitted with heaters to melt the plastic. It is constructed to endure high pressures and temperatures.
3. Extruder Screw: A critical component that transports the plastic pellets from the hopper to the barrel’s far end. Its rotation not only moves the pellets but also generates the heat needed to melt them through friction.
4. Heaters: Positioned along the barrel, these elements assist the screw in melting the plastic and maintain the required temperature for successful extrusion.
5. Die: This custom-designed part shapes the molten plastic. It is tailored specifically to match the product’s desired profile.
6. Cooling System: Post-extrusion, the shaped plastic must be cooled and solidified. This system can include elements like fans, water baths, or cooling rollers.
7. Cutter: This tool segments the newly formed plastic into desired lengths and can range from a simple guillotine to a more intricate rotary cutter, depending on the product specifications.
Plastic Extrusion Machine Operating
The operation of a plastic extruder involves a systematic procedure to ensure efficient production of plastic products. The first step is to load the plastic pellets into the hopper, set the temperature control of the machine, and switch on the heater. The plastic is melted in the barrel and pushed towards the die head by the extruder screw. It is vital to ensure that the temperature and speed of the extruder screw are set correctly to achieve the desired quality of the end product. Once the molten plastic has passed through the die, it takes the desired shape. It is then cooled and solidified in a cooling system before being cut into specified lengths by a cutting machine. It is important to note that the smooth operation of a plastic extruder requires constant monitoring and timely adjustments to maintain optimum output and quality.
Downstream equipment in plastic extrusion
Downstream equipment in plastic extrusion pertains to the array of machinery deployed post-extrusion to apply final modifications to the product. This equipment performs various crucial functions such as cooling, cutting, pulling, and winding to enhance the final attributes of the extruded plastic. Key types of downstream equipment include:
Cooling Tanks: These units are essential for cooling the extruded plastic to solidify and stabilize its shape. The cooling medium—either chilled water or air—is selected based on the plastic type and the specifications of the final product.
Pullers: These mechanisms ensure the extruded plastic maintains consistent speed and tension, critical for achieving uniform shape and size throughout the product. Available in various forms, such as belt pullers and roller pullers, they cater to different extrusion needs.
Cutters: After the cooling phase, cutters are employed to trim the extruded product to required lengths, ensuring precision in final measurements.
Coilers or Winders: For products such as tubes or profiles, coilers or winders collect the output on spools or reels, facilitating easier handling and transport.
Screen Printers: For products that need printed details or branding, screen printers are utilized to apply designs directly onto the surface of the extruded plastic.
The selection of downstream equipment is tailored to the specific type of product, material properties, and production demands. This equipment is integral to the extrusion process, playing a pivotal role in ensuring that the final product adheres to the set quality standards and meets precise specifications.
Considerations when choosing a machine
Productivity: High-capacity machines produce more product in less time, resulting in lower unit costs and a higher return on investment.
Energy Consumption: Machines with low energy consumption can significantly reduce operating costs and increase ROI.
Maintenance costs: Frequent maintenance can lead to increased costs and production downtime. Therefore, machines that require less maintenance can improve ROI.
Versatility: Machines that can process a wide range of plastic materials can meet a variety of production needs, increasing profitability.
Lifespan: The longer a machine’s lifespan, the higher the return on investment, as the initial investment can be spread over more production units.
Resale value: If the machine maintains a high resale value, the return on investment will increase.
Type of straw extrusion machine
In terms of material: there are pp straw extrusion machine, PLA straw extrusion machine, PHA straw extrusion machine,
In terms of main screw diameter: 50 mm and 65 mm main screws are available for the production of different diameter ranges of straw.
In terms of straw colour: single colour, two colour, two colour co-extrusion, three colour and three colour co-extrusion straw extrusion machine
Extruded pipe diameter adjustment
To precisely adjust the diameter of a pipe produced by an extrusion machine, various factors and settings must be meticulously managed and optimized:
1. Die and Calibrator Settings:
– Confirm that the calibrator is correctly aligned and sized, usually 3-5% larger than the target pipe diameter.
– Modify the die gap to suit the required pipe diameter. Increasing the gap enlarges the diameter, whereas reducing the gap decreases it.
2. Pressure Fluctuations:
Unstable compressed air can lead to uneven wall thickness in the pipe. This suggests that fluctuations in internal air pressure can cause variations in the pipe’s diameter or wall thickness
3. Extruder Throughput and Temperature:
– Alter the extruder throughput—decreasing it will reduce the pipe diameter, while increasing it will enlarge the diameter.
– Optimize the temperature settings of the extruder to ensure a consistent melt flow and prevent complications such as pipe sagging that can alter the diameter.
4. Traction Speed:
– Modify the haul-off unit’s speed. Accelerating the traction speed decreases the pipe diameter, while slowing it increases the diameter.
5. Cooling System:
– Adjust the cooling system, specifically the water flow and temperature in the cooling tanks, to guarantee even cooling. Non-uniform cooling can cause fluctuations in the pipe diameter.
6. Tooling and Sizing Equipment:
– Choose appropriate tooling for the specified pipe dimensions and ensure it is well-maintained and accurately calibrated.
By meticulously managing these parameters, the diameter of the pipe from the extrusion machine can be effectively controlled and precisely adjusted to meet specific requirements.
كيجي الآلات الموصى بها
Explore more machines from KEZHI


لماذا تختار كيجي
مرحباً بكم في KEZHI، شريككم الموثوق به في مجال آلات إنتاج وتعبئة القش المتقدمة. ومع التركيز على الابتكار والجودة ورضا العملاء، فإننا نقدم حلولاً مخصصة تعزز الكفاءة والإنتاجية. تم تصميم معداتنا المعتمدة عالية الأداء لتلبية المعايير الدولية، مما يضمن الموثوقية والفعالية من حيث التكلفة. انضم إلى العدد المتزايد من الشركات المصنعة في جميع أنحاء العالم الذين يثقون في KEZHI لتحويل عمليات الإنتاج الخاصة بهم وتحقيق نجاحهم.
مهمة
تحقيق رضا العملاء من خلال تحسين العمليات والمنتجات والخدمات باستمرار لضمان تلبية أو تجاوز المتطلبات باستمرار.
رؤية
ليتم الاعتراف بها كشركة رائدة في مجال الآلات من خلال الجودة الفائقة لمنتجاتنا وخدماتنا وموظفينا.
Main screw 50 mm, output 45 kg/hour, 80-100 kg/hour with 65 mm main screw.
To find the number of straws, divide by the weight of a single straw.
Industrial chiller: suggest 5HP chiller
Air compressor: 7.5KW is enough for one extrusion line, suggest 15KW for potential machine increasing in future
380V 50Hz 3Phase
الخيارات الأخرى متوفرة ، فقط اتصل واعطينا متطلباتك
نحن نوفر قطع الغيار ، فقط التقط صورة للجزء المطلوب ونرسلها إلينا وسنمنحك تكاليف اقتباس وساعي.
يمكننا عادة تسليم الجهاز في غضون 35 يومًا من تلقي الإيداع ،
نعم ، يمكننا تقديم مثل هذه التدريبات ، ويمكن توفير مقاطع الفيديو ، ويمكن أن يأتي فريقك أيضًا إلى مصنعنا للحصول على التدريب
This machine can work with PP,PLA,PHA,etc.
تعبئة الحالات الخشبية اختيارية ، ونقترح تعبئة الحالات الخشبية لتحميل الحاويات الأقل ،
يعتمد على طلبك ، هناك عدة خيارات لك.
أقل تحميل حاويات ، تحميل حاوية كامل (20 جيجابت/40 جيجابت)
International Express للعناصر الصغيرة
الضمان: 14 شهرًا من تاريخ الصعود إلى الصعود ، ويغطي المكونات الرئيسية مثل العاكس ، والمحرك ، وما إلى ذلك ، لا يتم تغطية الأجزاء.
بعد المبيعات: نقدم الدعم اللازم أثناء الإنتاج والتقنية والقطع الغيار.
يوصى بصيانة منتظمة ، والحفاظ على نظافة الماكينة ، واتبع دليل المحرك.
تحقق مما إذا كانت حالة تزييت التروس والمحامل جيدة في الوقت المناسب
يحصل الإجابات على أسئلتك
ستساعدك هذه الأسئلة المتداولة في كثير من الأحيان ، والتحقق من ذلك الآن