Maschine zur Herstellung von Kunststoffstrohhalmen
Are you looking for a machine to manufacture plastic straws or tubes? KEZHI offers you quality assurance, reliability and excellent value.
Kezhi -Maschinen können Ihnen eine hervorragende Produktionslinie bieten, um Ihr Projekt zu einem Erfolg zu machen.
Die Produkte KEZHI Bietet Sie an
Kezhi ist ein führender Hersteller, der sich auf die Entwicklung und Produktion verschiedener Strohmaschine, Strohverpackungsmaschine und Strohbiegermaschine spezialisiert hat. Unser Engagement für Qualität hat uns als Anbieter von erstklassigen Strohproduktionslösungen auf globaler Ebene positioniert
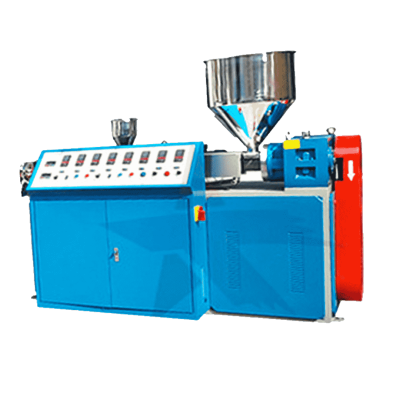
Plastikstrohmaschine
- Hauptschraubendurchmesser 65 mm/50 mm
- Delta Wechselrichter, WN -Motor,
- Maximum output 45kg/hour
- Suitable for PP straw making
- Auto material loader
Allgemein Anwendungen Für die Produktionslinie
Die Linie kann verwendet werden, um nicht nur Strohhalme der Getränke, sondern auch Kaffee -Rührer, Lutscherstöcke, Düsenrohre, Stift Nachfüllungen und andere kleine Profile durch Wechseln der Formen zu machen und mehr Optionen für Ihre Produktion zu bieten.
Einführung des Maschine
The PP (Polypropylene) straw making machine is a state-of-the-art, high-efficiency production line designed for manufacturing high-quality drinking straws from polypropylene material. This machine integrates advanced technology and superior engineering to deliver consistent, reliable performance, making it an ideal choice for businesses looking to produce straws in large quantities.
Hauptkomponenten
1. **Extruder**:
– **Function**: Melts and extrudes the polypropylene material into straw tubes.
– **Features**: Equipped with a high-performance screw and barrel, temperature control system, and a powerful motor for smooth and efficient extrusion.
2. **Mould Head**:
– **Function**: Shapes the extruded polypropylene into uniform straw tubes.
– **Features**: Precision-engineered mould heads that can be easily changed to produce straws of different diameters and thicknesses.
3. **Cooling System**:
– **Function**: Rapidly cools the extruded straws to retain their shape and strength.
– **Features**: Typically includes a water cooling tank with adjustable temperature controls to ensure optimal cooling.
4. **Haul-off Unit**:
– **Function**: Pulls the cooled straws from the extrusion line at a consistent speed.
– **Features**: Adjustable speed settings and precision rollers to handle straws gently and maintain their quality.
5. **Cutting Unit**:
– **Function**: Cuts the continuous straw tube into individual straws of desired lengths.
– **Features**: High-speed cutting mechanism with length control and smooth, burr-free cutting edges.
6. **Collector and Stacker**:
– **Function**: Collects and stacks the finished straws for easy packaging.
– **Features**: Automated systems to arrange and stack straws efficiently, minimizing manual handling.
The PP straw making machine is the perfect solution for businesses looking to enhance their production capabilities and meet the growing demand for polypropylene straws. With its superior performance, flexibility, and ease of operation, this machine stands out as a top choice in the straw manufacturing industry.

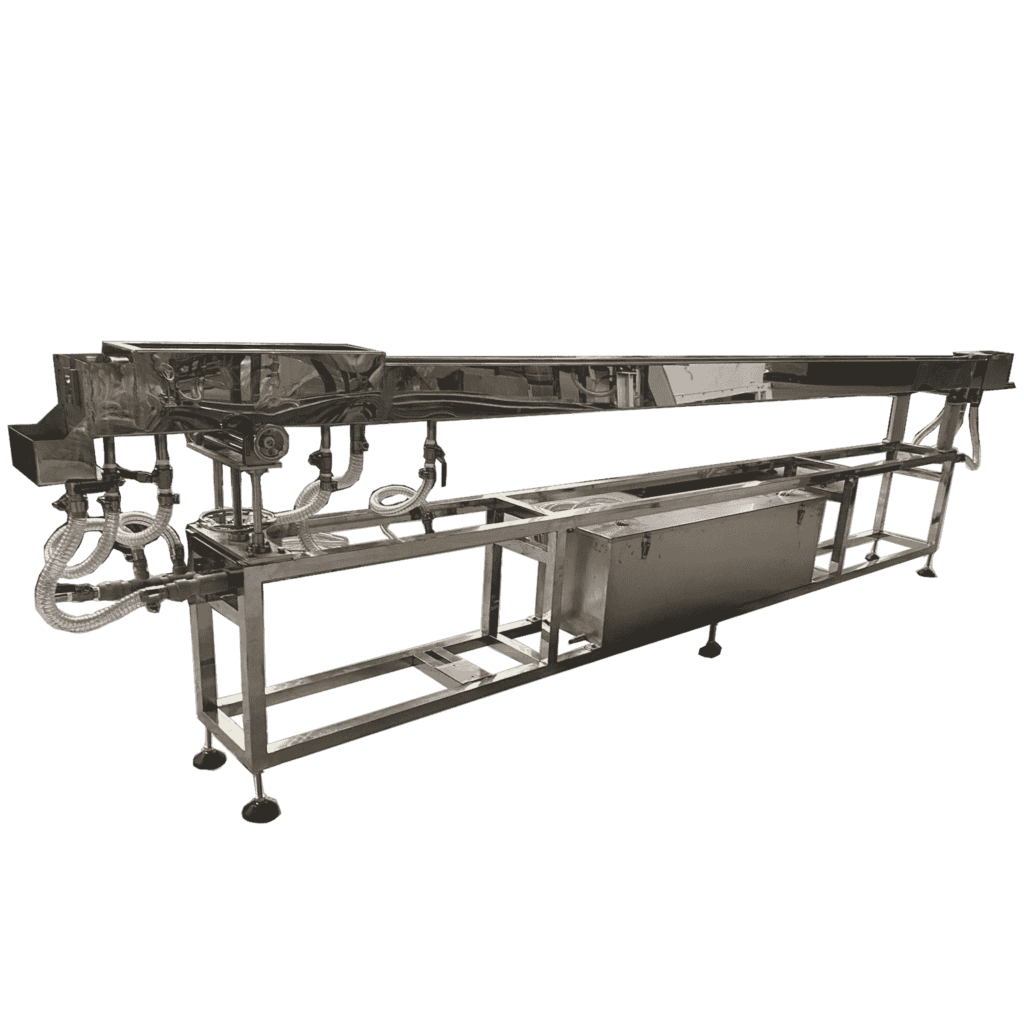


Merkmale von Extruder
Der wichtigste Teil der Produktionslinie, wo der Schlauch extrudiert wird
Temperaturregelung
Infrared heating, which is fast and gentle heating, dedicated to the production of high-end pipes, and does not cause secondary damage to the extruded material.
Hauptschraube
Spezielle 65 mm/50 -mm -Schraube, um das Merkmal von Bioplastikmaterial zu erfüllen.
L/D: 33: 1
meets the production of PP materials.
Mould Head
Precision-engineered mould heads that can be easily changed to produce straws of different diameters and thicknesses.
Two moulds will be offered with machine
Antriebsmotor
Mit einem 11-kW/ 30-kW-Dreiphasen-Asynchronmotor ist das Ausgangsdrehmoment größer, die Produktion ist stabiler, das Produkt ist ausgereift und leicht zu warten.
Servo Motor optional
Ausrüstungsreduzierer
Spezialverhärteter Zahnradreduzierer für Plastik -Extruder, Marke Guomao, zuverlässige Qualität,
Verhältnis 12,5
Wechselrichter
Delta Wechselrichter, berühmte Marke, stabile und zuverlässige Leistung, der bekannteste Wechselrichter in der Strohindustrie
Kühlwassersenke Merkmale
Im zweiten Teil der Linie wird das extrudierte Rohr hier abgekühlt und besser geformt.
- Material
Edelstahl, kein Rost, längeres Leben
- Wassertank
Mit einem Wassertank ausgestattet, können Sie sich direkt mit dem Wasserkühler verbinden
- Verstellbarkeit
Die Richtung des Kühlwassers kann eingestellt werden,
- Länge
Zwei Optionen, 3,5 Meter und 4,5 Meter
- Temperatur erforderlich
Die Wassertemperatur im Wasserwaschbecken muss 25 bis 30 Grad betragen (für PP-Material)


Traktion & Schneidemaschine Merkmale
Im dritten Teil der Linie wird das extrudierte Rohr hier gezogen und in kleine Stücke geschnitten.
- Ende schneiden
Die Maschine kann Enden in verschiedenen Winkeln schneiden, um unterschiedliche Anforderungen zu erfüllen
- Geschwindigkeitseinstellung
Adjustable speed of pulling & cutting to make different lengths of straws
- Stroh Traktion
Diese Maschine kann abhängig von Ihrem Strohmaterial PP/ PLA eine Riementraktion oder eine Walzentraktion haben
Erforderlich Zusatzausrüstung
Diese beiden Maschinen sind für die Produktionslinie erforderlich.

Industriekühler
Für die Produktionslinie ist ein 5-PS-Industriekalt erforderlich. Sie können einen luftgekühlten Kalt oder einen wassergekühlten Kältemittel nach Ihren Bedürfnissen auswählen. Durchflussanforderung: über 3 Kubikmeter pro Stunde

Luftkompressor
Für eine einzelne Produktionslinie ist ein 10 -PS -Luftkompressor erforderlich. Sie können einen Pistolenluftkompressor oder einen Schraubluftkompressor für Ihre Bedürfnisse auswählen.
Wie es Arbeiten
Aus diesem Video finden Sie heraus, wie es funktioniert,
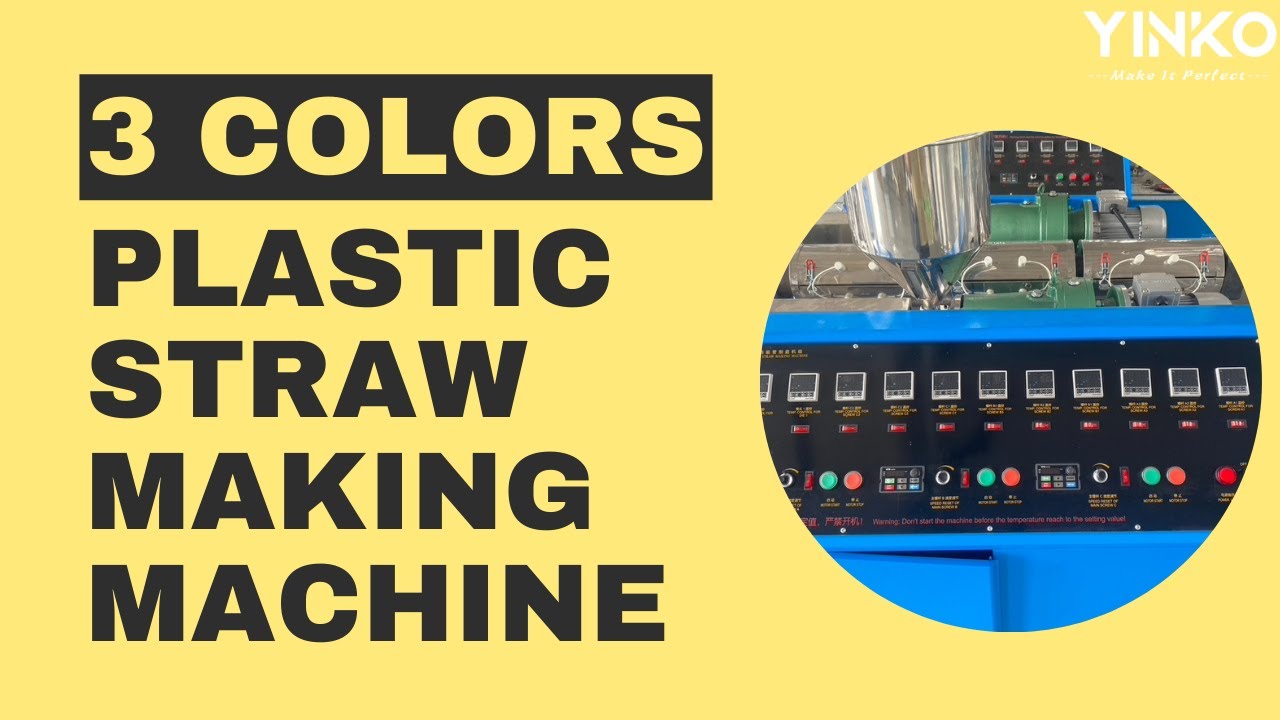
Maschine Spezifikationen
Find some specifications of the plastic straw production line
Modell | KZ-011-50 | |
---|---|---|
Stromversorgung | Hauptschraube | 380V,3Phase,50HZ, 7.5KW(VFD) |
Sub-Screw | / | |
Heating | 9KW | |
Hauling motor | 0.75KW(VFD) | |
Cutting Motor | 0.75KW(VFD) | |
Total Power | 18KW | |
Extruder | Main Screw diameter | 50mm |
Screw L/D | 28:1 | |
Gearbox | ZLY133 | |
Temperature controller | 5 SETS | |
Motor | WANMAN | |
Gear reducer | GUOMAO | |
Wechselrichter | DELTA | |
Electric control cabinet | 1 set | |
Kühlwassersenke | Länge | 4.5meters |
Material | 304 Steel stainless | |
Water storage tank | 1 set | |
Blow dry device | 1 set | |
Traktion & Cutting Unit | Traction unit | 1set |
Cutting unit | 1set | |
motor | 0.75KW(VFD) *2 | |
Ende schneiden | 90°/60°/45° | |
PLC control | Optional | |
L -förmige Strohhalmmaschine | Optional | |
Air compressor | 7.5KW(10HP) | |
Industrial chiller | 5HP, water cooled / air cooled |
Die Basis Wissen Um Kunststoff -Extrusionsmaschine
Eine kurze Einführung in Plastik -Extruder, mit denen Sie ein grundlegendes Verständnis der Maschine erhalten können
Inhaltsverzeichnis
Was ist Plastik -Extrusionsmaschine?
Die Kunststoff-Extrusion ist eine hochvolumige Herstellungstechnik, bei der roher Kunststoff, typischerweise in Pelletform, geschmolzen und in ein kontinuierliches Profil extrudiert wird. Der Prozess initiiert, wenn das Harz in den Trichter des Extruders geladen wird und sich in den Lauf hinunterzieht, wo es zunehmend erhitzt wird, bis es schmilzt. Anschließend treibt ein Schraubmechanismus den geschmolzenen Kunststoff durch einen Würfel an, der ihn in die erforderliche Form formuliert. Während es abkühlt und festigt, nimmt es die endgültige Form verschiedener Produkte an, die von Rohren und Plastikfolien bis hin zur Wetterstreifen bis zur Drahtisolierung reichen. Diese Methode wird in verschiedenen Branchen für ihre Effizienz, Vielseitigkeit und konsistente Fähigkeit, große Volumina herzustellen, hoch geschätzt.
Arbeitsprinzip des Plastik -Extruders
Die Rolle von Extrudern bei der Plastikextrusion
Extruder dienen als Kernkomponente im Kunststoff -Extrusionsprozess, der hauptsächlich aus einem beheizten Lauf mit einer rotierenden Schraube besteht. Der Prozess beginnt mit der Einführung von rohen Kunststoffmaterialien, typischerweise in Pelletform, in den Extruder über einen Trichter. Während sich die Schraube dreht, treibt sie die Pellets in den Lauf vor, wo sie auf erhebliche Wärme und Druck stoßen und dazu führen, dass sie in eine viskose Flüssigkeit schmilzen. Dieser flüssige Kunststoff wird dann durch einen Würfel extrudiert - ein Werkzeug, das so konstruiert ist, dass der Kunststoff in das angegebene Profil aus der Maschine entsteht. Das Kunststoffprodukt wird anschließend abgekühlt und verfestigt und behält seine Form bei, da es in vorbestimmte Längen segmentiert ist. Diese Methode ist entscheidend für die Erzeugung kontinuierlicher Plastiklängen in verschiedenen Formen und spielt damit eine entscheidende Rolle in verschiedenen industriellen Anwendungen.
Komponenten einer Kunststoff -Extrusionsmaschine
Eine Standard -Kunststoff -Extrusionsmaschine besteht aus mehreren Schlüsselkomponenten, die jeweils eine entscheidende Rolle im Extrusionsprozess spielen:
1. HOPPER: Der anfängliche Einstiegspunkt für das Rohstoffmaterial, in der Regel in Pelletform. Der Trichter kann das Material in den Fass des Extruders übertragen.
2. Barrel: Diese Komponente umhüllt die Extruderschraube und ist mit Heizungen ausgestattet, um den Kunststoff zu schmelzen. Es ist gebaut, um hohen Drücken und Temperaturen zu ertragen.
3. Extruderschraube: Eine kritische Komponente, die die Plastikpellets vom Hopper zum fernen Ende des Fass transportiert. Seine Rotation bewegt nicht nur die Pellets, sondern erzeugt auch die Wärme, die erforderlich ist, um sie durch Reibung zu schmelzen.
4. Heizungen: Diese Elemente befinden sich entlang des Laufs und unterstützen die Schraube beim Schmelzen des Kunststoffs und halten die erforderliche Temperatur für eine erfolgreiche Extrusion bei.
5. sterben: Dieser maßgeschneiderte Teil prägt den geschmolzenen Kunststoff. Es ist speziell auf das gewünschte Profil des Produkts zugeschnitten.
6. Kühlsystem: Nach der Extrusion muss der geformte Kunststoff abgekühlt und verfestigt werden. Dieses System kann Elemente wie Lüfter, Wasserbäder oder Kühlrollen umfassen.
7. Cutter: Dieses Werkzeug unterteilt den neu gebildeten Kunststoff in die gewünschten Längen und kann je nach Produktspezifikationen von einer einfachen Guillotin bis zu einem komplizierteren Drehschneider reichen.
Kunststoff -Extrusionsmaschine Betrieb
Der Betrieb eines Kunststoff -Extruders beinhaltet ein systematisches Verfahren, um eine effiziente Produktion von Kunststoffprodukten sicherzustellen. Der erste Schritt besteht darin, die Plastikpellets in den Trichter zu laden, die Temperaturregelung der Maschine einzustellen und die Heizung einzuschalten. Der Plastik wird im Lauf geschmolzen und durch die Extruderschraube in Richtung des Kopfes gedrückt. Es ist wichtig sicherzustellen, dass die Temperatur und Geschwindigkeit der Extruderschraube korrekt eingestellt werden, um die gewünschte Qualität des Endprodukts zu erreichen. Sobald der geschmolzene Kunststoff durch den Würfel gefahren ist, hat er die gewünschte Form. Es wird dann in einem Kühlsystem abgekühlt und verfestigt, bevor es durch eine Schneidemaschine in bestimmte Längen geschnitten wird. Es ist wichtig zu beachten, dass der reibungslose Betrieb eines Kunststoff -Extruders eine konstante Überwachung und zeitnahe Anpassungen erfordert, um eine optimale Ausgabe und Qualität aufrechtzuerhalten.
Downstream -Geräte in der Plastikextrusion
Nachgeschaltete Geräte in der Kunststoffextrusion bezieht sich auf das Array von Maschinen, die nach der Extrusion eingesetzt wurden, um endgültige Änderungen an das Produkt anzuwenden. Diese Ausrüstung führt verschiedene entscheidende Funktionen aus wie Kühlung, Schneiden, Ziehen und Wickeln, um die endgültigen Eigenschaften des extrudierten Kunststoffs zu verbessern. Zu den wichtigsten Arten der nachgeschalteten Geräte gehören:
Kühltanks: Diese Einheiten sind für das Abkühlen des extrudierten Kunststoffs unerlässlich, um seine Form zu verfestigen und zu stabilisieren. Das Kühlmedium - entweder gekühltes Wasser oder Luft - wird basierend auf dem Kunststofftyp und den Spezifikationen des Endprodukts ausgewählt.
Pullers: Diese Mechanismen sorgen dafür, dass der extrudierte Kunststoff eine konsistente Geschwindigkeit und Spannung beibehält, was für die Erzielung einer gleichmäßigen Form und Größe im gesamten Produkt entscheidend ist. Erhältlich in verschiedenen Formen, wie z. B. Riemenabziehern und Rollenabfertigern, richten sich an unterschiedliche Extrusionsbedürfnisse.
Schneider: Nach der Kühlphase werden Schneider verwendet, um das extrudierte Produkt auf die erforderlichen Längen zu trimmen, um die Präzision bei den endgültigen Messungen zu gewährleisten.
Spulen oder Wickler: Für Produkte wie Röhrchen oder Profile sammeln Spulen oder Wicker die Ausgabe an Spulen oder Rollen und erleichtern die leichtere Handhabung und den Transport.
Bildschirmdrucker: Für Produkte, die gedruckte Details oder Branding benötigen, werden Bildschirmdrucker verwendet, um Entwürfe direkt auf die Oberfläche des extrudierten Kunststoffs anzuwenden.
Die Auswahl der nachgeschalteten Geräte ist auf die spezifische Art von Produkt, Materialeigenschaften und Produktionsanforderungen zugeschnitten. Diese Ausrüstung ist ein wesentlicher Bestandteil des Extrusionsprozesses und spielt eine zentrale Rolle bei der Gewährleistung des Endprodukts an den festgelegten Qualitätsstandards und erfüllt genaue Spezifikationen.
Überlegungen bei der Auswahl einer Maschine
Produktivität: Maschinen mit hoher Kapazität produzieren in kürzerer Zeit mehr Produkte, was zu niedrigeren Kostenkosten und einer höheren Kapitalrendite führt.
Energieverbrauch: Maschinen mit geringem Energieverbrauch können die Betriebskosten erheblich senken und den ROI erhöhen.
Wartungskosten: Häufige Wartung kann zu erhöhten Kosten und Produktionsausfallzeiten führen. Daher können Maschinen, die weniger Wartung erfordern, den ROI verbessern.
Vielseitigkeit: Maschinen, die eine breite Palette von Kunststoffmaterialien verarbeiten können, kann eine Vielzahl von Produktionsanforderungen erfüllen und die Rentabilität erhöhen.
Lebensdauer: Je länger die Lebensdauer einer Maschine, desto höher ist der Return on Investment, da die anfängliche Investition über weitere Produktionseinheiten verteilt werden kann.
Wiederverkaufswert: Wenn die Maschine einen hohen Wiederverkaufswert beibehält, steigt die Kapitalrendite.
Art der Stroh -Extrusionsmaschine
In Bezug auf Material: Es gibt eine PP -Stroh -Extrusionsmaschine, die PLA -Stroh -Extrusionsmaschine, die Pha -Stroh -Extrusionsmaschine,
In Bezug auf den Hauptschraubendurchmesser: 50 mm und 65 mm Hauptschrauben sind für die Herstellung von Strohhalmen mit unterschiedlichem Durchmesser erhältlich.
In Bezug auf die Strohfarbe: Einzelfarbe, zwei Farbe, zwei Farbkoextrusion, drei Farbe und drei Farb-Coextrusion-Stroh-Extrusionsmaschine
Extruded Rohrdurchmessereinstellung
Um den Durchmesser eines von einer Extrusionsmaschine erzeugten Rohrs genau anzupassen, müssen verschiedene Faktoren und Einstellungen akribisch verwaltet und optimiert werden:
1. Einstellungen für Sterbe und Kalibrator:
– Bestätigen Sie, dass der Kalibrator korrekt ausgerichtet und dimensioniert ist, normalerweise 3-5% größer als der Zielrohrdurchmesser.
– Ändern Sie den Stempelspalt, um den erforderlichen Rohrdurchmesser zu entsprechen. Das Erhöhen der Lücke vergrößert den Durchmesser, während die Verringerung der Lücke ihn verringert.
2. Druckschwankungen:
Instabile Druckluft kann zu einer ungleichmäßigen Wandstärke im Rohr führen. Dies deutet darauf hin, dass Schwankungen des inneren Luftdrucks Schwankungen des Rohrdurchmessers oder der Wandstärke verursachen können
3. Extruder -Durchsatz und Temperatur:
– Ändern Sie den Extruderdurchsatz - dankraut wird er den Rohrdurchmesser verringern und gleichzeitig den Durchmesser vergrößern.
– Optimieren Sie die Temperatureinstellungen des Extruders, um einen konsistenten Schmelzstrom zu gewährleisten und Komplikationen wie Rohrsacken zu verhindern, die den Durchmesser verändern können.
4. Traktionsgeschwindigkeit:
– Ändern Sie die Geschwindigkeit der Abklebereinheit. Die Beschleunigung der Traktionsgeschwindigkeit verringert den Rohrdurchmesser und erhöht den Durchmesser.
5. Kühlsystem:
– Stellen Sie das Kühlsystem, insbesondere den Wasserfluss und die Temperatur in den Kühltanks, ein, um eine gleichmäßige Kühlung zu gewährleisten. Eine ungleichmäßige Kühlung kann Schwankungen im Rohrdurchmesser verursachen.
6. Werkzeug- und Größengeräte:
– Wählen Sie eine geeignete Werkzeug für die angegebenen Rohrabmessungen und stellen Sie sicher, dass sie gut gepflegt und genau kalibriert ist.
Durch akribisch verwaltetes Management dieser Parameter kann der Durchmesser des Rohrs von der Extrusionsmaschine effektiv gesteuert und genau angepasst werden, um spezifische Anforderungen zu erfüllen.
KEZHI Empfohlene Maschinen
Entdecken Sie mehr Maschinen von Kezhi


Warum wählen KEZHI
Willkommen bei Kezhi, Ihrem vertrauenswürdigen Partner für fortschrittliche Strohproduktion und Verpackungsmaschinen. Mit einem Fokus auf Innovation, Qualität und Kundenzufriedenheit liefern wir maßgeschneiderte Lösungen, die die Effizienz und Produktivität verbessern. Unsere zertifizierte Hochleistungsgeräte sind so konzipiert, dass sie internationale Standards entsprechen und die Zuverlässigkeit und Kosteneffizienz gewährleisten. Schließen Sie sich der wachsenden Anzahl von Herstellern weltweit an, die dem Kezhi vertrauen, um ihre Produktionsprozesse zu verändern und ihren Erfolg voranzutreiben.
Mission
Erreichen Sie die Kundenzufriedenheit, indem Sie Prozesse, Produkte und Dienstleistungen kontinuierlich verbessern, um die Anforderungen konsequent zu erfüllen oder zu übertreffen.
Vision
Als führender Maschinenhersteller durch die überlegene Qualität unserer Produkte, Dienstleistungen und Personal anerkannt zu werden.
Main screw 50 mm, output 30 kg/hour, 45 kg/hour with 65 mm main screw.
Um die Anzahl der Strohhalme zu finden, teilen Sie sich durch das Gewicht eines einzelnen Strohhalms.
Industrial Chiller: Schlagen Sie 5 PS -Kühler vor
Luftkompressor: 7,5 kW reicht für eine Extrusionslinie aus. Hegen Sie 15 kW vor, dass potenzielle Maschine in Zukunft zunimmt
380 V 50 Hz 3Phase
Weitere Optionen sind verfügbar, kontaktieren Sie einfach und geben Sie uns Ihre Anforderungen
Wir liefern Ersatzteile, machen Sie einfach ein Foto des erforderlichen Teils und senden es uns an, und wir geben Ihnen ein Angebot und eine Kurierkosten.
Wir können die Maschine normalerweise innerhalb von 35 Tagen nach Erhalt der Kaution liefern.
Ja, wir können solche Schulungen bereitstellen, Videos können bereitgestellt werden, Ihr Team kann auch in unsere Fabrik kommen, um Schulungen zu erhalten
Diese Maschine kann mit PP, PLA, PHA usw. arbeiten.
Die Packung von Holzfällen ist optional, und wir empfehlen Holzfälle für weniger Behälter Laden.
Hängt von Ihrer Bestellung ab, es gibt mehrere Optionen für Sie.
Ladung weniger Container, Vollcontainerbelastung (20gp/40gp)
International Express für kleine Gegenstände
Garantie: 14 Monate ab dem Datum des Boarding, und es deckt wichtige Komponenten wie Wechselrichter, Motor usw. ab. Das Tragen von Teilen ist nicht abgedeckt.
After Sales: Wir bieten die notwendige Unterstützung während Ihrer Produktion, des technischen und teile Angebots.
Eine regelmäßige Wartung wird empfohlen, die Maschine sauber halten und dem Motorhandbuch folgen.
Überprüfen Sie, ob der Schmierstatus von Zahnrädern und Lagern zu gegebener Zeit gut ist
Erhalten Antworten zu Ihren Fragen
Diese häufig gestellten Fragen helfen Ihnen ebenfalls, lesen Sie sie jetzt aus