- Why is controlling air pressure essential for straw production?
- What temperature should you maintain during extrusion?
- How does the extrusion process affect straw diameter?
- What do material properties do to help with straw extrusion?
- More Related Questions
- 1. What role does the water bath play in keeping the diameter of the straw?
- 2. How does the puller help shape the drinking straw?
- 3. What happens when air pressure is inconsistent during extrusion?
- 4. Why is it important to control temperature during the extrusion process?
- Need some help in straw production? contact us for a solution!
- نتیجه گیری
- درباره KEZHI
Ensuring the diameter of drinking straws is consistent during the extrusion process is essential for producing quality products. Straws with inconsistent diameter do not meet standards, are not of uniform strength, and are defective. As a straw manufacturing professional, I’ll explain the critical elements you need to maintain to achieve consistency.
You must control several critical factors to maintain a consistent diameter during the extrusion process. We can produce straws that are uniform in diameter by managing air pressure, extrusion rates, temperature, and material properties. Each of these factors contributes to the finished product in its way.
The air pressure is the most critical factor to monitor.
It controls the internal structure of the straw. The constant air stream keeps the straw round and helps the diameter stay consistent. Even small changes in air pressure can cause the diameter to change, especially with straws with thin walls. We must constantly monitor and adjust the air pressure during production.
Why is controlling air pressure essential for straw production?
- Air pressure control prevents the straw from collapsing.
- The steady airflow contributes to a uniform diameter.
- Small variations in pressure can cause noticeable diameter changes.
- Adjusting air pressure changes both the inner and outer diameter of the straw.
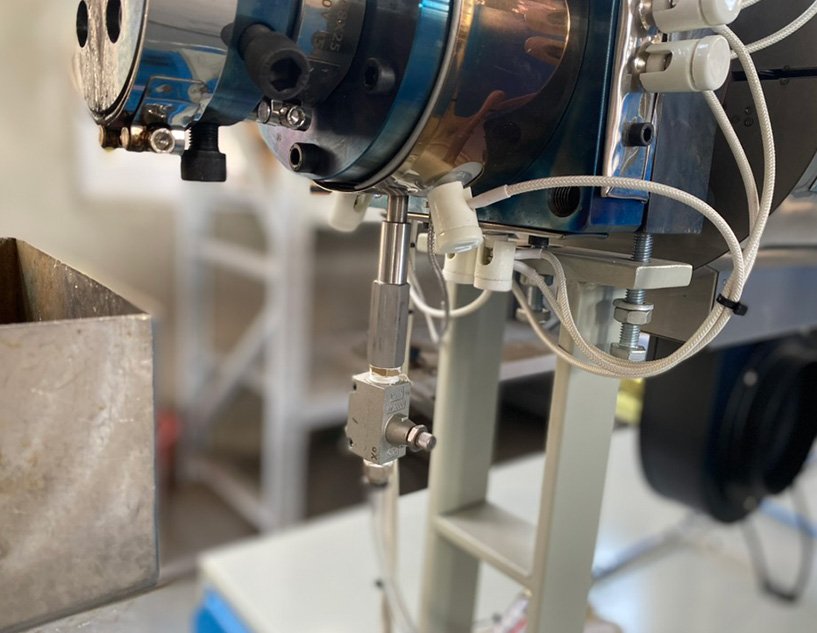
Another key factor in diameter control is temperature maintenance. Temperature affects the flow of the plastic material. When the temperature is steady, the material flows through the die properly without warping or shrinking. Too much temperature variation will cause uneven cooling and diameter changes.
You need to regularly adjust the heaters and use cooling fans to keep the temperature constant. Monitoring temperature will help you to keep the diameter consistent on each straw and minimize unwanted defects.
What temperature should you maintain during extrusion?
- Maintaining the correct temperature ensures proper plastic flow.
- Material overheating can cause it to be thinned out or have inconsistent thickness.
- Heating the extrusion steadily prevents it from warping or shrinking.
- Consistent cooling aids in making the diameters stable.

The extrusion process and equipment also affect the diameter of the finished product. The resin pellets that are typically used as a raw material are melted and pushed through the extruder by a screw. When the melted resin comes out of the end of the die, it takes the shape of the straw. You need a “puller” to help keep the straw’s shape and get it through the cooling system to maintain consistency.
The cooling system takes the straw and cools it so it holds its shape and diameter. You need to make sure that the water temperature in the bath is properly maintained to ensure that the straw cools uniformly and doesn’t vary in diameter.
How does the extrusion process affect straw diameter?
- The screw mechanism pushes the resin to the die to shape it.
- The puller maintains the straw shape as it travels through the cooling system.
- Water cooling helps the straw maintain its shape and diameter.

Material considerations also come into play. To achieve consistent results, you have to control the extrusion rate and ensure that the wall thickness is uniform. When the wall thickness is consistent, the material cools uniformly, which helps prevent warping or twisting. Understanding how the raw materials you use behave is critical to achieving a uniform diameter.
You also have to maintain your equipment and set up your machines properly to avoid problems with extrusion. Proper calibration of machines helps prevent issues with inconsistent heating and wall thickness.
What do material properties do to help with straw extrusion?
- The thickness of the material affects how quickly it cools and stays consistent in diameter.
- The better quality resins give you more control over extrusion.
- Poorer quality materials can lead to some inconsistency in diameter.

More Related Questions
1. What role does the water bath play in keeping the diameter of the straw?
The water bath is critical to keeping the diameter of drinking straws during the extrusion process. Here’s how it helps:
- It cools and solidifies the molten plastic that’s extruded through the die to form the straw.
- The water bath provides a consistent temperature to ensure that the straw cools evenly. If the straw does not cool evenly, it can warp or not be the same thickness all the way along, which affects the diameter.
- Quickly cooling the extruded straw in the water bath helps prevent it from deforming. If the straw stays hot too long, it can deform and won’t have a consistent diameter.
In summary, the water bath helps to cool the plastic quickly to achieve the desired diameter and keep the straw from deforming.
2. How does the puller help shape the drinking straw?
The puller is a critical part of the straw manufacturing process and is very important in shaping the straw. Here’s how it works:
- It pulls the straw along. When the straw comes out of the die, it is still hot and soft and can be easily deformed. The puller helps to pull the straw steadily and evenly to maintain its shape.
- It maintains tension on the straw as it gets pulled so that it doesn’t sag and collapse. This tension is important in keeping the diameter and wall thickness consistent on the straw.
- It works with sizing plates in some straw manufacturing situations. The puller pulls the straw through the sizing plates where it can be shaped and sized correctly.
- It helps the straw transition to the cooling stage (usually the water bath) after being shaped by the puller.
In summary, the puller helps shape drinking straws by pulling them along, maintaining tension, helping with diameter sizing, and transitioning to the cooling stage.
3. What happens when air pressure is inconsistent during extrusion?
When air pressure is inconsistent during extrusion, it can cause a lot of problems that affect the quality of the end product:
- Surface defects will occur because the molten plastic won’t flow evenly, thus causing surface imperfections (ripples, waves) on the extruded straws.
- Dimensionally, the end product won’t be accurate because inconsistent material (caused by air pressure fluctuations affecting flow rate) will cause dimensions to change. For example, if the air pressure drops suddenly, it may leave thinner spots. If it increases, it can cause thicker areas and the overall product dimensions won’t be accurate.
- Bubbles or voids can suddenly form inside the extruded material if the air pressure drops suddenly.
- Under increased air pressure at the die, you can have die swell where the extrudate expands unexpectedly when it comes out of the die. This affects the shape and makes it difficult to get tight tolerances and control the size.
- With irregular air pressure, you can cause a melt fracture. This is a turbulent flow of molten plastic that occurs because of irregular pressure, causing rough surfaces (often referred to as sharkskin).
- Inconsistent air pressure can affect cooling rates, which in turn can affect flexibility versus brittleness. Uneven cooling can cause stress concentrations in the material itself.
In summary, maintaining consistent air pressure is vital to producing quality products with consistent dimensions, smooth surfaces, and good structural integrity. Variability in air pressure creates a lot of defects.
4. Why is it important to control temperature during the extrusion process?
Temperature control is very important during the extrusion process for several reasons:
- You must have uniform melting of the plastic material. It is critical to have the plastic melt uniformly so you have uniform properties (strength, flexibility, etc.) in the finished product. If the temperature is low, not all the material will melt, which can lead to bubbles, etc.
- The temperature has a direct effect on the flow characteristics of the molten plastic. Properly maintaining the temperature allows for optimal flow through the extruder, thus reducing friction and allowing smoother processing. This can lead to higher production rates and increased efficiency.
- Different plastics melt and have thermal stability ranges. You can cause the material to degrade if you exceed the temperatures required for processing. When you exceed these ranges, the material can discolor and lose mechanical properties.
- It can help you be energy efficient. While higher temperatures can help you run faster, it also can dramatically increase your energy costs to run those higher temperatures. So, it’s important to keep the temperatures where they need to be to minimize energy consumption while running at maximum throughput.
- It can help you with safety. Overheating can create fires or toxic emissions. Having effective temperature control systems can help mitigate these issues.
- It will provide consistency and quality control. Temperature variations will affect wall thickness and the surface finish of the extruded products, which can impede functionality and appearance.
Need some help in straw production? contact us for a solution!
In summary, effective temperature control during extrusion is required for uniform melting, proper flow characteristics, material integrity, energy efficiency, safety concerns, and consistent quality in your finished product.
نتیجه گیری
By controlling air pressure, temperature, and extrusion rates, you can keep the diameter consistent on your drinking straws. Doing the right things will allow you to make quality products and reduce defects.
درباره KEZHI
KEZHI is a leading manufacturer specializing in the design and production of high-quality straw making machines, including plastic, biodegradable, and paper straw production lines. With a strong R&تیم و امکانات تولیدی پیشرفته ، Kezhi متعهد به ارائه راه حل های نوآورانه ، قابل اعتماد و کارآمد برای مشتریان در سراسر جهان است. طیف گسترده ای از محصولات ما ، همراه با خدمات استثنایی پس از فروش و پشتیبانی فنی ، ما را به عنوان یک شریک قابل اعتماد در صنعت تولید نی قرار می دهد. در Kezhi ، ما به کمک به مشتریان خود با ارائه راه حل های متناسب که نیازهای خاص آنها را برآورده می کند ، کمک می کنیم.